Strata Miniatures
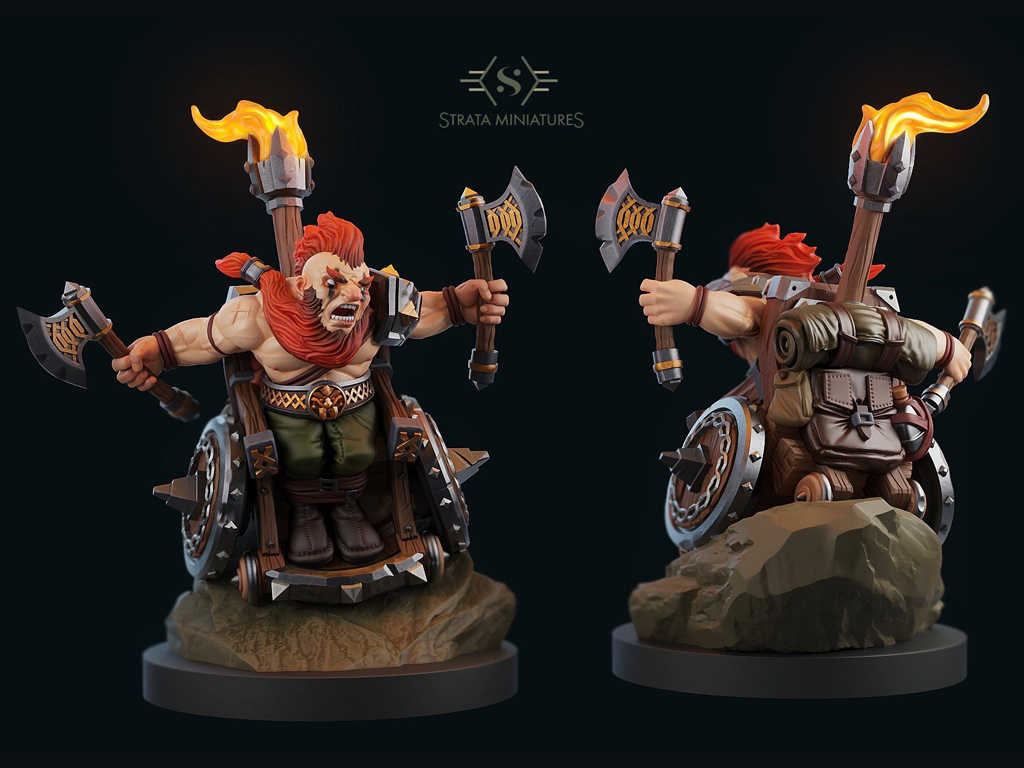
Client: Strata Miniatures
Design: Russ Charles
Format: n / a
Material: 3D design
Strata Miniatures
Fanatic tabletop game players want to take their sets to the next level and personalize it. Strata Miniatures allows the players to have their own costum tokens made. Special coins or point counters with your own text or logo that make the game experience even more special. Strata Miniatures offers the service to design and print these parts in 3D.
Collaboration with De Tinnen Roos
In 2020 Strata Miniatures started the Dungeons and Diversity project. A game expansion of Dungeons & Dragons where disabled characters in wheelchairs are given a place in the original game. Strata Miniatures asked De Tinnen Roos to cast the various miniatures. Russ Charles, the designer of the characters, has been working with De Tinnen Roos for some time as designer of Guildball (Steamforged Games).
We produce thousands of miniatures for table top games!
Looking for a producer for your pewter or thermoplastic resin game miniatures?
De Tinnen Roos thinks along with you in the development of your game. From 3D design to production.
Please feel free to contact us for the possibilities and a quotation.
Dungeons and Diversity
Expansion on Dungeons & Dragons
Dungeons & Dragons is a worldwide known game and is played by more than 13 million players. The number of characters and associated miniatures for this game continues to grow. Yet there is a group of players who are not represented in the game; the disabled player in a wheelchair. In Strata Miniatures’ Dungeons and Diversity, for the first time this group of players is aknowledged and becomes inclusive in the game. This game expansion brings various characters with different powers into play, but in a special combat wheelchair that suits the character. Dungeons and Diversity is not a standalone game, but is an extension of the existing game and brings its own rules around the characters that can be integrated into the original game.
Why characters in a wheelchair?
Dungeons & Dragons players might ask the question, “Why would anyone need a wheelchair? This world has magic!” Sara Thompson, who wrote the story behind Dungeons and Diversity and is in a wheelchair herself, has a good answer:
“We recommend that you read Salvatore’s” Drizzt “novels. In addition, healing spells such as recovery and regeneration are very expensive to play, and what about those who are simply born with a disability? You cannot regenerate or restore what was not there. And some of us? Well, we don’t want to be “fixed.” This chair was never made to make a disabled character “better” than an able-bodied character. It was created to enable characters with disabilities to experience the same adventure as a able-bodied character. Not as a valid character, but as a character that suits them and that means a character in a wheelchair. Having a disability is not something to be ashamed of. These miniatures give the disabled player the opportunity to see themselves in the tabletop game and enjoy it even more. ”
(not the exactly words Sara used)
Expansion with a mission
Not only does the game provide disabled players with a character to mirror themselves, but it has also given itself a social purpose. When purchasing the miniatures, Strata Miniatures donates 25% of thepurchase to the Ehlers-Danlos foundation.
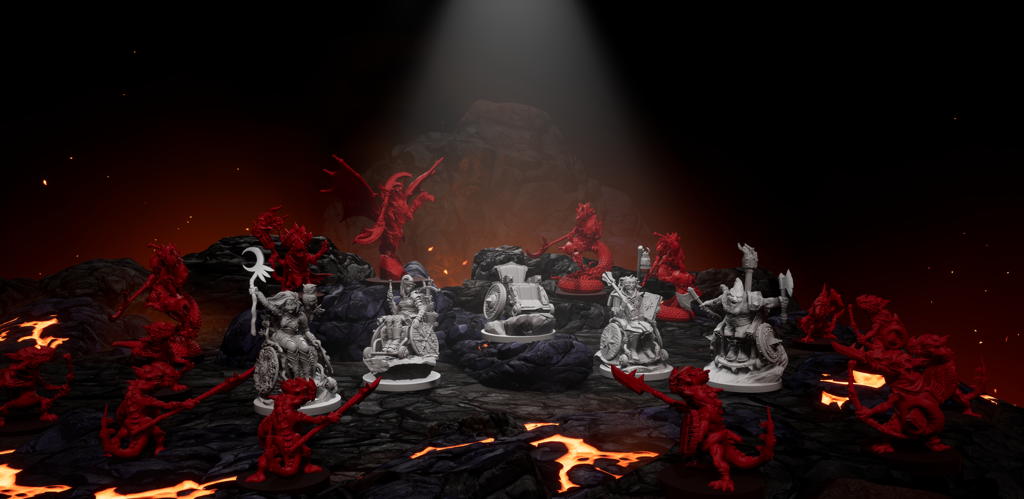
Techniques
Design and model
3d designs on the computer
While designing the Dungeons and Diversity miniatures, Russ Charles created 3D designs based on Sara Thompson’s personal descriptions. Through previous collaborations, Russ knows exactly how the figures are molded at De Tinnen Roos. That is why the design has already taken into account how the miniatures come out of the mold. Before the 3D files are sent, the miniatures are already “cut” into separate parts which the player can assemble after purchase.
3D printing
We were able to make the completed 3D drawing tangible at De Tinnen Roos with the Asiga 3D printer. The parts are built up layer by layer. A frame is printed on the sides of the parts to ensure that the hot mass does not collapse during printing. Before the prints can be used to make the masters, the frames are cut loose and the objects are thoroughly cleaned with alcohol.
Mold making and casting
Making masters
The 3D prints were used to make metal masters. All parts are placed in a silicone rubber mold. The masters are cast with bismuth on our Nicem spincasting machine. We use this metal because it is stronger during the making of the production molds. Parts do not bend when pressed into the soft silicone.
Making production molds
With the help of the bismuth masters, several production molds were made for two casting systems. The characters, wheelchairs and weapons are cast in tin and have been given a mold for the Nicem spincasting machine. The basis for the miniatures is cast in thermoplastic resin in our SiOCAST injection molding machine and that requires a different type of mold. Both types of molds are made in-house.
Casting
With several craftsmen on the work floor, the casting of both the metal and the plastic parts is done at the same time. Each casting is manually poured in tin or filled with thermoplastic resin. Despite the use of casting machines, every production remains largely manual work.
Finishing
Cutting metal minis
Once the metal miniatures come out of the mold, they are cut from the sprew. Casting channels and venting channels are removed from the miniatures with a pair of nippers so that they can be delivered clean. Any membranes are removed with a knife. These membranes arise, for example, when the pressure on the mold is not optimal, but do not cause any loss of quality.
Cutting resin objects
The resin objects are cut from the wreath with nippers. Unlike the tin parts, this must always be cut, otherwise you will get visible fractures. The cut spots are brushed with a sanding block and small irregularities are polished away.
Quality control
Quality control is done continuously during the production process. During the cutting of the sprew, while casting, the first quality check is done. Miniatures and parts that are not completely filled up immediately disappear into the melting pot or go into the shredder for reuse. During the cutting there is the second quality check. The person who cuts, checks whether all parts are in good order and that no damage occurs during cutting. Parts that are ready are placed in rows on trays and checked again by someone during a final check before packing. During this check, the number of parts is immediately counted again so that the correct number is delivered.